Schneller, größer, sparsamer: Der Neue für den Untergrund
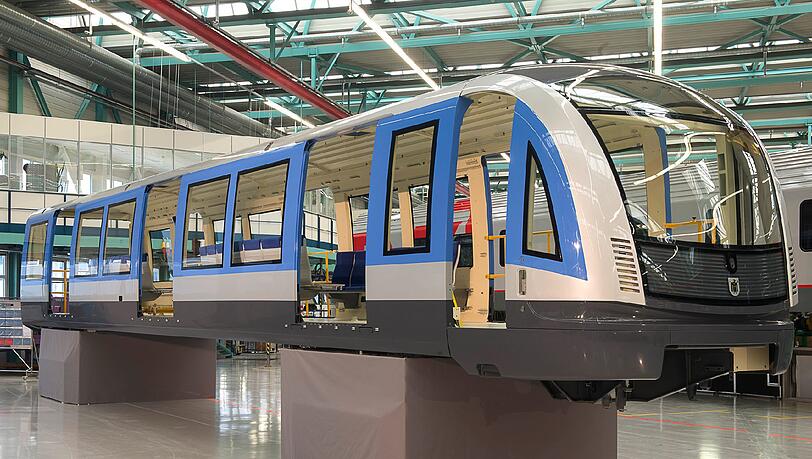
WIEN - Da steht er, der Piefke. An den Außenseiten leicht gewölbt, das gläserne Vorderteil sieht aus wie ein Bienenschädel. Breit und großkopfert – ein echter Münchner.
Rund um die Fenster ist alles „RAL DS-270 50 40“. Das ist die Kennung für das Blau der Münchner Verkehrsgesellschaft (MVG). Dazu kommen Graphitgrau und Weißaluminium, über allem Klarlack. Alles von Hand aufgetragen im Siemens-Werk in Wien.
In Halle 320 steht der erste Kopfwagen aufgebockt. MVG-Chef Herbert König streckt die Hand aus, fast muss er sich auf die Zehenspitzen stellen. Er streicht mit der Hand über den Rahmen. Vorsichtig. Ist ja noch ganz neu, der C2. Und nicht billig.
185 Millionen Euro hat die MVG für ihre neue U-Bahn- ausgegeben. Noch nie hat die MVG mehr für neue Fahrzeuge investiert. Die 21 Züge des Typs C2 sollen die alten aus der Zeit von 1970 bis 1975 ersetzen und den Takt auf besonders ausgelasteten Strecken verstärken. Zum Fahrplanwechsel im Dezember 2013 soll der erste C2 fahren.
Wenn alles gut klappt, darf Siemens bis 2016 und 2020 noch einmal 46 Stück liefern – für insgesamt über eine halbe Milliarde Euro.
Die Anforderungen waren klar: Der Neue sollte schneller, wirtschaftlicher und ökologischer sein. Mit mehr Platz. Und mehr Design.
Aus Sicht der MVG hat Siemens das geschafft. „Der Zug ist sehr schön, das passt schon“, sagt König. Mit 4500 PS fährt der C2 jetzt Tempo 90 statt 80. Beschleunigt schneller. Spart Energie durch LEDs. Lässt sich laut Siemens zu 95 Prozent recyceln. Beim Bremsen produziert er sogar Strom, den er zurück ins Netz speist.
Die Werbetafeln über den Fenstern sind wie im Vorgängermodell C1 verschwunden. Über dem Gang hängen Monitore, die die nächsten Haltestellen und die Anschlüsse in Echtzeit anzeigen. Dazu kommen MVG-Filmchen. Eine Sendeschleife ist 15 Minuten lang, „davon sind 15 Prozent Werbung“, sagt MVG-Chef König – also 2,25 Minuten.
In den Waggons haben jetzt 28 Menschen mehr Platz, insgesamt 940 Passagiere passen in einen Zug. Sie kommen durch die breiteren Türen schneller rein und raus und verteilen sich im Zug besser. Alle Sitze sind gepolstert, sie ersetzen auch die rutschigen Holzbänke des Vorgängermodells. Die waren nicht so wartungsfreundlich, wie die MVG gedacht hatte.
Der C2 könnte sogar führerlos fahren – die Technik ist ab Werk eingebaut. MVG-Chef König will ihn aber weiter von Menschen steuern lassen, noch jedenfalls. „So ein Zug hat 40 Jahre Lebensdauer, da kann sich viel ändern.“
Ein Zug besteht aus 780 000 Einzelteilen, allein im Kopfwagen mussten die rund 70 Konstrukteure 22 Kilometer Kabel verlegen und jedes Rohr, jede Schraube und jede Abdeckung so platzieren, dass sie Platz spart, trotzdem funktioniert und irgendwie zum Konzept des Münchner Designers Alexander Neumeister passt.
Das zu planen, war ein 180 Tonnen schwerer und 114 Meter langer Albtraum. Deshalb haben die Konstrukteure den C2 zunächst komplett virtuell gebaut. Im 3D-Computermodell konnten sie prüfen, ob die Türöffnungsanlage wirklich in den engen Kasten passt. Oder ob man kaputte Sitzreihen am Stück durch die Zugtüren bekommt. Als alles passte, gingen die Daten direkt an Maschinen, die alles genau so herstellten, wie es im PC steht.
Den Zug zu bauen, ist im Prinzip recht einfach. Zuerst fräsen die Arbeiter das Untergestell zurecht. Dann schweißt ein Roboter die Seitenwände und das Dach dran – jetzt steht der Wagenrahmen, sechs Tonnen schwer, komplett aus Aluminium, das teilweise selbst recycelt ist. „Ihre letzte Red-Bull-Dose ist da auch sicher dabei“, sagt ein Konstrukteur.
Danach packen die Arbeiter den Rahmen mit weiteren 24 Tonnen voll: Motoren aus Nürnberg, Fahrwerke aus Graz, Seitenfenster aus Italien, Frontscheiben aus Frankreich. Die Sitze stammen aus Kiel, die Monitore aus Bergamo, die Elektrotechnik aus der Oberpfalz und die Innenverkleidung aus Qingdao, China. Das alles dauert 75 Tage, 200 Arbeiter haben eine Hand dran.
Beim ersten Wagen fügten die Siemens-Arbeiter noch eine kleine Wiener Note hinzu. Um den Bau zu feiern, aßen sie alle zusammen in der Werksalle ein deftiges Mahl: Es gab Schnitzel.